- Магия металла: Путешествие от безликой проволоки до идеального болта
- Анатомия производства: Заглянем в самое сердце завода
- КЛЮЧЕВЫЕ ЭТАПЫ РОЖДЕНИЯ КРЕПЕЖА
- Этап 1: Формовка. Холодная высадка против горячей штамповки
- Этап 2: Накатка резьбы. Рождение сцепления
- Этап 3: Термообработка. Закаляя характер
- Этап 4: Нанесение покрытия. Броня от коррозии
- Этап 5: Контроль качества. Без права на ошибку
Задумывались ли вы когда-нибудь, что общего у вашего офисного стула, гигантского моста через реку, детского конструктора и космического спутника? Ответ прост и в то же время гениален: их объединяют маленькие, но невероятно важные детали — крепежные изделия. Болты, гайки, винты, шпильки… Мы настолько привыкли к их существованию, что совершенно не замечаем, а ведь без них наш технологичный и комфортный мир буквально рассыпался бы на части. Это безмолвные титаны, которые несут на себе колоссальную ответственность, оставаясь в тени более крупных и заметных конструкций.
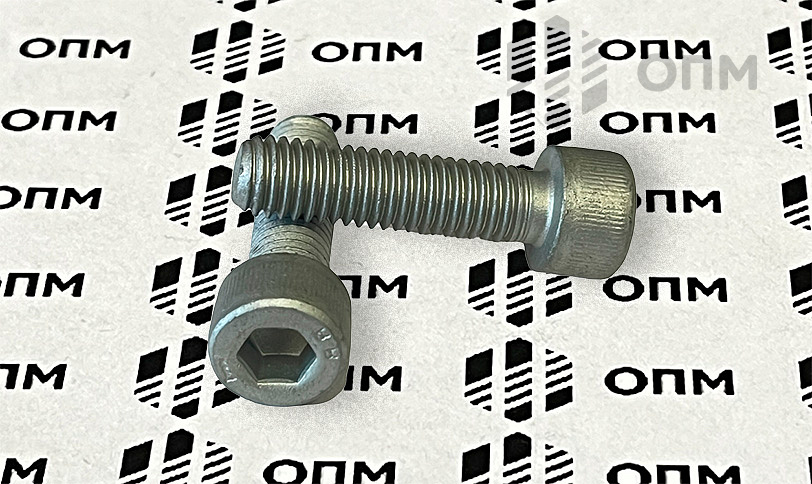
Но как появляется на свет обычный стальной болт? Неужели его просто вытачивают из куска железа, как скульптор высекает статую из мрамора? Процесс его рождения намного интереснее и технологичнее, чем можно себе представить. Это настоящее путешествие, полное удивительных трансформаций, где бесформенный моток проволоки под давлением в сотни тонн обретает знакомые нам очертания, закаляет свой характер в огне и покрывается защитной броней. Это история о том, как наука и инженерная мысль превращают простой металл в основу надежности. Давайте вместе пройдем этот путь от начала и до конца и раскроем все секреты производства этих незаменимых помощников.
Магия металла: Путешествие от безликой проволоки до идеального болта
Представьте себе моток стальной проволоки, который называется катанка. На первый взгляд, в нем нет ничего особенного. Просто длинная металлическая нить, свернутая в огромную бухту. Она еще не знает, кем станет в будущем: крошечным винтиком в смартфоне или мощным анкерным болтом в фундаменте высотного здания. Пока это лишь сырье, заготовка, полная скрытого потенциала. Словно глина в руках гончара или тесто в руках пекаря, она ждет своего часа, чтобы преобразиться. И этот процесс преображения начинается с тщательной подготовки. Нельзя просто взять и начать «лепить» болт. Сначала нужно подготовить «холст».
Первый этап этого путешествия — очистка. Проволока, прибывшая с металлургического комбината, покрыта окалиной — тонким слоем оксидов, который образуется при высоких температурах прокатки. Окалина твердая и абразивная. Если ее не убрать, она, словно наждачная бумага, будет беспощадно изнашивать дорогостоящее оборудование на последующих этапах. Поэтому бухты с катанкой отправляются в специальную «ванну» — процесс травления. Их погружают в раствор кислоты (обычно серной или соляной), которая деликатно растворяет окалину, не затрагивая сам металл. После кислотной ванны проволока тщательно промывается, чтобы смыть остатки агрессивного вещества, и проходит через процесс нейтрализации. Теперь она чистая, но это еще не все.
Далее следует этап, который можно сравнить с работой ювелира, — волочение. Очищенная проволока все еще имеет не совсем точный диаметр и недостаточно качественную поверхность для дальнейшей обработки. Процесс волочения заключается в том, что проволоку протягивают через ряд последовательно уменьшающихся отверстий — фильер. Каждая следующая фильера чуть меньше предыдущей. Это похоже на то, как вы пропускаете тесто через насадки мясорубки, чтобы получить спагетти идеальной толщины. В результате волочения проволока не только приобретает строго заданный калибр с точностью до сотых долей миллиметра, но и меняет свою внутреннюю структуру. Металл уплотняется, его поверхность становится гладкой и блестящей. Он становится прочнее и пластичнее одновременно — идеальное состояние для следующего, самого главного акта этого производственного спектакля.
Перед основной обработкой на проволоку наносят специальное подсмазочное покрытие. Это может быть фосфатирование или омыление. Зачем это нужно? Представьте, что вам нужно протолкнуть что-то через очень узкое отверстие. Если вы смажете поверхность, дело пойдет гораздо легче. Точно так же и здесь. Это покрытие служит смазкой, которая снижает трение в момент формовки будущего изделия, защищает инструмент от износа и обеспечивает высокое качество поверхности самого крепежа. Теперь наша проволока полностью готова. Она прошла очищение, обрела идеальную форму и покрылась защитным слоем. Из безликой катанки она превратилась в высококачественную заготовку, из которой вот-вот, буквально за доли секунды, родится новое изделие. Она стоит на пороге самого главного своего превращения, где холодный металл поддастся колоссальной силе и примет ту форму, которую задумал инженер. Этот момент — кульминация всей предварительной подготовки, и от него зависит, насколько качественным и надежным будет будущий болт или винт.
Анатомия производства: Заглянем в самое сердце завода
Мы подготовили нашу проволоку, и теперь начинается самое интересное — ее превращение в готовое изделие. Этот процесс напоминает работу сложнейшего организма, где каждый орган выполняет свою четкую функцию. Сердцем этого организма являются огромные и шумные станки, способные за один удар многотонного пресса придать металлу нужную форму. Существует два основных метода, которыми пользуются инженеры для создания крепежных изделий, — холодная высадка и горячая штамповка. Выбор метода зависит от размера, материала и сложности будущего изделия. Именно на этом этапе безликий отрезок проволоки превращается в узнаваемый крепеж из стали, готовый занять свое место в сложнейших механизмах и конструкциях.
Давайте разберем весь производственный цикл по косточкам, чтобы понять, как из простого материала получаются высокотехнологичные метизы. Это не просто механическая штамповка, а выверенный до мелочей технологический балет, где у каждого движения есть своя цель и смысл.
КЛЮЧЕВЫЕ ЭТАПЫ РОЖДЕНИЯ КРЕПЕЖА
Весь путь от проволоки до блестящей гайки можно разделить на несколько важнейших стадий. Каждая из них вносит свой вклад в итоговые характеристики продукта: его прочность, точность и долговечность.
Этап 1: Формовка. Холодная высадка против горячей штамповки
Это момент истины, когда заготовка обретает свою первичную форму.
- Холодная объемная штамповка (высадка): Это основной метод для производства стандартного крепежа массовых серий (болты, винты, саморезы, заклепки) небольших и средних размеров.
- Как это работает? Подготовленная проволока подается в специальный холодновысадочный автомат. Машина отрезает от нее кусок нужной длины, и затем серия последовательных ударов пуансонов (подвижных инструментов) по заготовке, зажатой в матрице (неподвижной форме), формирует сначала стержень, а затем и головку будущего болта. Весь процесс происходит при комнатной температуре и занимает доли секунды.
- Преимущества:
- Высочайшая производительность: Автоматы могут «выстреливать» сотни готовых изделий в минуту.
- Экономия материала: Это безотходное производство, здесь нет стружки. Весь металл идет в дело.
- Повышенная прочность: За счет наклепа (уплотнения структуры) металл в процессе деформации становится прочнее.
- Горячая штамповка: Этот метод применяют для изделий больших диаметров, сложных форм или для крепежа из специальных сплавов, которые плохо поддаются обработке в холодном состоянии.
- Как это работает? Заготовки (уже не проволока, а нарубленные прутки) нагреваются в индукционных печах до температуры 1100-1250°C. При такой температуре сталь становится пластичной, как пластилин. Раскаленную заготовку помещают в пресс-форму, где мощный пресс одним или несколькими ударами придает ей необходимую форму.
- Преимущества:
- Возможность создавать крупные и сложные детали.
- Меньшие требования к пластичности исходного материала.
Этап 2: Накатка резьбы. Рождение сцепления
После того как у нас получилась «болванка» с головкой и стержнем, ей нужно нарезать резьбу. И здесь тоже есть свой секрет. Резьбу не нарезают резцом, как на токарном станке, а накатывают.
- Процесс накатки: Заготовку прокатывают между двумя плоскими или круглыми плашками (роликами), на которых уже есть резьбовой профиль. Они с огромным усилием вдавливаются в стержень болта, не срезая металл, а уплотняя его и формируя витки резьбы.
- Почему это лучше? Накатанная резьба значительно прочнее нарезанной. Волокна металла не перерезаются, а изгибаются, повторяя профиль резьбы, что создает более прочную и износостойкую поверхность.
Этап 3: Термообработка. Закаляя характер
Для ответственных конструкций требуется высокопрочный крепеж. Чтобы придать изделиям нужный класс прочности (например, 8.8, 10.9, 12.9), их подвергают термообработке.
- Закалка: Изделия нагревают до высокой температуры (около 850-900°C), а затем резко охлаждают в масле или воде. От этого сталь становится очень твердой, но хрупкой.
- Отпуск: Чтобы снять хрупкость, крепеж снова нагревают, но уже до более низкой температуры (350-600°C), и выдерживают некоторое время. После этого он приобретает оптимальное сочетание твердости, прочности и пластичности.
Этап 4: Нанесение покрытия. Броня от коррозии
Чтобы защитить стальной крепеж от ржавчины, его покрывают тонким слоем другого металла. Самый распространенный метод — гальваническое цинкование. Изделия погружают в ванну с электролитом, и под действием электрического тока на их поверхности осаждается ровный и блестящий слой цинка. Цинк принимает удар коррозии на себя, защищая стальную основу.
Этап 5: Контроль качества. Без права на ошибку
На каждом этапе производства — от проверки исходной проволоки до осмотра готовой партии — работает отдел технического контроля. Специалисты проверяют геометрию изделий, качество резьбы, прочностные характеристики и толщину защитного покрытия. Только после строгого контроля партия получает «путевку в жизнь».
- Coil Coating — Преимущества перед традиционной окраской
- Запчасти для спецтехники 2025: секреты выбора оригинальных деталей и экономия на обслуживании
- Котельное оборудование: виды, характеристики и применение в промышленности
- Ремонт техники Apple в 2025: Все что нужно знать каждому владельцу
- Автопогрузчик: Ваш железный помощник в мире грузов – выбираем технику с умом
- Плазменная резка металла: ключевые области применения в промышленности и искусстве
- Поставки металлопроката: как выбрать надежного поставщика и оптимизировать затраты
- Сдать вторсырье в Екатеринбурге: как превратить мусор в ресурс и помочь планете
- Червячные хомуты: Секрет надежного соединения, о котором вы не задумывались
- Средства индивидуальной защиты в цеху: что использовать, чтобы вернуться домой целым и невредимым?