- Секреты контакто-электрической резки: как искра меняет производство
- EDM: детали, преимущества и скрытые тонкости
- Основные принципы EDM и их значение
- Где эта технология наиболее эффективна?
- Преимущества, которые вдохновляют производителей
- Какие риски стоит учесть?
- Неочевидные аспекты, о которых мало говорят
- Организация рабочего места и экология
- Как правильно выбрать EDM-станок?
Наша главная тема — электроэрозионная резка металла и её роль в современной промышленности. Возможно, вы уже сталкивались с упоминанием этого уникального способа, слышали о его точности или видели, как деталь сложнейшей формы появляется буквально «из искры». Давайте разберёмся во всех тонкостях, чтобы окончательно понять, почему данный метод считается столь перспективным и востребованным.
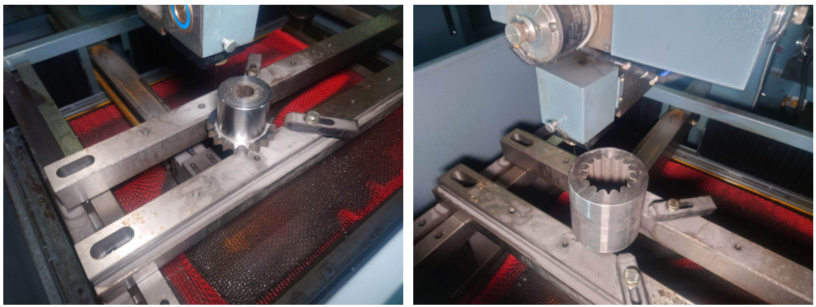
Секреты контакто-электрической резки: как искра меняет производство
Чтобы понять, в чём заключается суть электроэрозионного процесса, давайте сделаем небольшой экскурс в теорию. Представьте себе: заготовка из твёрдой основы и проволока, между которыми проходит череда электрических разрядов. Эти разряды напоминают крохотные молнии, каждую из которых сложно разглядеть глазом. Однако именно они «выбивают» крошечные фрагменты металла (назовём этот материал твёрдой деталью или жёстким сплавом, чтобы не повторяться) и формируют нужный контур. Звучит футуристично, правда? Но в реальности такой метод применяется уже десятки лет, причём сейчас он развился до уровня прецизионной точности.
В отличие от привычных способов механического воздействия — когда фрезы, сверла или абразивные круги снимают слой за слоем, — при электроискровом варианте ключевым рабочим инструментом становятся именно электрические импульсы. Они высвобождают значительное количество тепла в микрообъёмах, что позволяет локально «расплавлять» и «выпаривать» нужные участки. Из-за минимального механического давления на изделие нет физических деформаций. Хорошо это или плохо? Определённо хорошо, ведь в результате удаётся сохранять первозданную геометрию и достигать того уровня точности, который порой невозможен при классической механической фрезеровке.
Однако, возможно, вы спросите: а для каких именно случаев стоит применять данный тип сегментирования заготовки? Вообще, электроэрозионная методика универсальна: с её помощью можно обрабатывать твёрдые сплавы, жаропрочные стали, а также цветные металлы (бронзу, латунь и прочие материалы). Данное направление ценят в авиастроении, медицинской сфере, автомобилестроении, производстве пресс-форм и штампов. Неудивительно, что найти оборудование для таких операций сегодня стремятся многие предприятия, в том числе Завод Металлоконструкций Спб, ведь оптимизированная процедура раскроя помогает добиваться сложных форм при минимальном количестве дефектов.
Давайте обратимся к конкретным преимуществам:
- Высокая точность
Благодаря тонкой проволоке (или специальному электроду) и микроскопической зоне воздействия достигается детальная геометрия. Иногда точность может составлять доли микрона, что особенно важно для изделий, требующих идеальной подгонки. - Низкая механическая нагрузка
При классической механической обработке часто возникает избыточная вибрация и давление. В нашем случае влияние сил трения сведено к минимуму, так как основной «инструмент» — это разряд. Поэтому даже сложные и хрупкие сплавы не растрескаются и не поведутся. - Меньше брака
Если вам важно снизить риск микротрещин или деформаций, то контактно-электрический способ будет хорошим решением. Фактически, при грамотном подборе параметров (скорости подачи, силы тока) деталь сохраняет максимально однородную структуру. - Возможность работы со сложным контуром
Представьте, что вам необходимо вырезать замысловатый орнамент на листе из жаропрочной стали. Традиционный станок с фрезой упирается в проблему избыточного нагрева режущего элемента и быстрой его выработки. А электроискровая установка, используя проволоку и импульс, без труда справится даже с самыми тонкими изгибами. - Отсутствие строгих ограничений по твердости
Есть детали, для которых механическая обработка затруднительна (например, закалённые или легированные сплавы повышенной прочности). Электроразрядный способ в данном случае оказывается более чем уместен, ведь для него главное — способность материала проводить электричество. Твердость же не играет ключевой роли.
Как видите, у данного технологического подхода масса достоинств. Но было бы несправедливо не упомянуть и о некоторых нюансах. Во-первых, процедура обычно требует достаточно сложного оборудования с системой ЧПУ (числовым программным управлением), а его стоимость не всегда доступна малым предприятиям. Во-вторых, процесс может происходить медленнее по сравнению с традиционными методами фрезерования или резки лазером, особенно если речь идёт об объёмной, глубокой обработке. Но когда нужна недостижимая другими способами точность, эти особенности перестают казаться критичными.
Ещё один интересный момент связан с использованием рабочей среды. В процессе формирования нужных отверстий или контуров вокруг зоны реза обеспечивается специальная диэлектрическая жидкость. Она выполняет сразу несколько функций: охлаждает место воздействия, отводит микрочастицы, стабилизирует искры и гарантирует равномерное распределение электроэнергии. Когда разряд «бьёт» по заготовке, тончайший слой этой жидкости мгновенно испаряется и даёт возможность формировать «микровзрыв», устраняя лишний фрагмент материала. Так происходит шаг за шагом, пока не будет достигнута желаемая форма. Согласитесь, в этом есть что-то волшебное, хотя всё объясняется законами физики.
Любопытно, что сегодня электроискровые установки могут работать как с массивными стержневыми электродами, так и с тончайшей проволокой. От выбранного инструмента зависит метод ведения процесса:
- Проволочно-вырезной (или по-другому проволочный) вариант. Здесь в качестве основного элемента используется очень тонкая металлическая нить (иногда настолько тонкая, что напоминает леску для рыбалки). Она движется вдоль заданной траектории и «прожигает» деталь по нужному контуру.
- Погружной (объёмный) тип. В этом случае берётся электрод определённой формы (например, цилиндр, пластинка, сложный 3D-контур), и с его помощью «вытачиваются» внутренние полости или фигурные углубления.
Но давайте подумаем, что же движет предприятиями, которые активно внедряют инновации в производство? Ведь всегда есть альтернатива — к примеру, лазерный раскрой, гидроабразив или плазменный способ. Однако электроискровая методика особенно хороша там, где требуется добиться сложной конфигурации в особо твёрдых материалах без потери качества кромок. Например, при создании пресс-форм для литья пластмасс важно выдержать точные габариты полостей, чтобы при выпуске серийной продукции каждый элемент получался идентичным, без зазоров и деформаций. И вот здесь волшебная «электрическая искра» играет решающую роль.
Если вы решите освоить данный вид обработки, можете встретить одно затруднение — подбор правильного оборудования. На рынке есть десятки производителей, но выбирать придётся с учётом специфики ваших задач и предполагаемого объёма работ. Можно вначале взять установку с более простой конфигурацией, а затем, при увеличении заказов, перейти к профессиональным многоосевым станкам. При этом важно позаботиться о квалифицированном операторе. Ведь в отличие от классического сверления или фрезерования здесь требуется понимание настроек силы тока, частоты импульсов, скорости протяжки проволоки и многих других параметров. Конечно, возможно освоить все нюансы и самостоятельно, но при работе с дорогостоящим оборудованием лучше иметь в штате подготовленного инженера.
Между прочим, когда речь заходит о крупном промышленном производстве, почти всегда возникает вопрос: а возможно ли подготовить заготовки с нужными характеристиками заранее, чтобы при поступлении заказа можно было без промедлений приступать к операции? Да, в ряде случаев заготовки действительно хранят на складе. Если вы хотите эффективно управлять производственным циклом, то наверняка знаете, как важно иметь под рукой серийные партии деталей. К примеру, кто-то предпочитает поковки купить заранее, чтоб потом не тратить время на дополнительное согласование поставщиков. Согласитесь, когда у вас всё под рукой, вы быстрее реагируете на запросы клиентов, экономите время и деньги.
Напоследок можно отметить, что электроэрозионные станки часто являются частью целого комплекса оборудования. На крупных предприятиях технологическая цепочка может включать механические фрезерные станки, лазерные комплексы, токарные автоматы и, собственно, электроискровые установки. Такая интеграция позволяет оптимизировать процесс и использовать подходящий метод для каждой стадии работы. Например, черновой съём излишков металла проводят на обычном фрезерном станке, а финишную доводку с точностью до микрона отдают во власть «искраобразующего» аппарата. Так достигается баланс между скоростью обработки и качеством итогового результата.
Таким образом, электроэрозионная технология — это не просто причудливая искромётная альтернатива стандартным методам, а полноценный инструмент для тех, кто стремится к точности, качеству и конкурентному преимуществу на рынке. Если у вас есть желания повысить уровень компетентности в производстве и предлагать заказчикам высокое качество, то электроискровая резка станет вашим верным союзником, причём надолго. Ведь, как говорится, прогресс не стоит на месте, а значит, мы можем ожидать ещё более впечатляющих разработок в этой сфере в ближайшем будущем.
EDM: детали, преимущества и скрытые тонкости
Этот раздел мы посвятим деталям. И под словом «детали» здесь понимаются не только металлические элементы сложной формы, но и мельчайшие аспекты, которые необходимо знать каждому, кто планирует внедрить электроразрядную обработку в своё производство. Приготовьтесь к более структурированному формату и визуальным акцентам, чтобы не упустить ни одного важного момента.
Основные принципы EDM и их значение
- Взаимодействие «электрод – заготовка»
В основе контактно-электрической технологии лежит принцип controlled spark erosion. Проще говоря, между двумя проводящими телами (электродом и заготовкой) в диэлектрической среде происходят кратковременные разряды.- Что это даёт?
Искра «выбивает» частицы твёрдой поверхности локально, практически без физического давления. Таким образом достигается высокая точность и сложность контуров. - Почему это важно?
Если в традиционных методах механический инструмент постоянно соприкасается с поверхностью, есть риск износа режущих кромок и даже поломок. В EDM же износ электрода или проволоки идёт относительно медленно, а сам обрабатываемый материал не испытывает сильных вибраций.
- Что это даёт?
- Роль диэлектрической жидкости
Иногда диэлектрик сравнительно мало обсуждают, хотя он имеет колоссальное значение для стабильности процесса. Попросту говоря, это вещество помогает формировать, контролировать и гасить искровые разряды.- К чему стоит быть готовым?
Нужно правильно подбирать тип жидкости (специальное масло или дистиллированная вода) и своевременно её очищать. Загрязнённая рабочая среда повышает риск дефектов и затрудняет отвод продуктов эрозии. - Какие преимущества?
Охлаждение зоны воздействия, удаление микрочастиц и создание особой среды для формирования разряда без разбрызгивания расплавленного сплава.
- К чему стоит быть готовым?
- Тонкости настройки силы тока и частоты импульсов
Чем тоньше нужно получить финишную деталь, тем аккуратнее настраивают энергетические параметры. Высокая сила тока ускоряет удаление лишнего участка, но снижает точность. Низкий ток даёт более ровную кромку, однако сама операция длится дольше.- Как найти баланс?
Всё зависит от целей: если вам надо быстро снять большой объём металла, возможен более грубый режим. Для финишной обработки включают маломощные разряды и тщательно следят за скоростью подачи проволоки (или электрода).
- Как найти баланс?
- Сложности при глубоком формообразовании
Когда вам нужно получить глубокую полость внутри заготовки, возможны проблемы с отводом отработанных частиц и охлаждением.- Совет:
Периодическое прерывание процесса с промывкой или продувкой области разряда помогает избежать перегрева и оседания эрозионных остатков на стенках детали.
- Совет:
Где эта технология наиболее эффективна?
- Пресс-формы и штампы
Здесь каждая доля миллиметра критична. Нужно воспроизвести рельеф, который при производстве пластмассовых деталей будет формировать внешний облик этих изделий. - Авиация и космос
Сложные узлы из особо твёрдых сплавов, способных выдерживать температурные и механические нагрузки, — именно та сфера, где лазер может не справиться или привести к дополнительной деформации. - Медицина
Хирургические инструменты и импланты порой имеют непростую форму и крайне жёсткие требования к чистоте обработки. Электрическая эрозия тут позволяет избежать микротрещин.
В каждом из перечисленных направлений EDM (Electrical Discharge Machining) выступает надёжным помощником, но только при корректной настройке оборудования и квалификации оператора.
Преимущества, которые вдохновляют производителей
- Отсутствие физических контактных усилий
Если сравнить с любыми механическими методами, где режущий инструмент давит на материал, то при электроискре значение прилагаемого давления практически отсутствует. - Аналитика и контроль
Современные EDM-станки имеют модуль ЧПУ. С его помощью задают траекторию движения электрода/проволоки, а система самостоятельно корректирует подачу. Это значит, что вы получаете стабильный результат без «человеческого фактора». - Экономия времени на сложных деталях
Да, звучит удивительно, ведь многие считают, что скорость такой эрозионной технологии невысока. Но если вам надо сделать криволинейный паз или крошечное отверстие в деталях, за которые не берутся традиционные фрезы, то итогом станет выигрыш по времени. Ведь другие методы могут вообще не подойти или потребовать дорогостоящей спецоснастки.
Какие риски стоит учесть?
- Цена оборудования
Для небольшого цеха покупка EDM-станка может стать серьёзным шагом, особенно если вы пока не уверены в постоянном потоке заказов. - Квалификация персонала
Неправильно выставленные параметры легко приводят к ухудшению качества кромки и увеличению времени обработки. Поэтому оператор должен разбираться в теории импульсных процессов, а также иметь практический опыт. - Расходные материалы
Проволока, электроды, диэлектрик — всё это требует регулярной замены и обслуживания. Халатное отношение к этим моментам ведёт к внезапным сбоям и браку.
Перед покупкой сложного станка полезно пройти небольшое обучение у производителя. Кроме того, стоит выделить отдельное пространство в цехе с системой фильтрации, поскольку при длительной работе возможны испарения технической жидкости и мелкая эрозионная пыль.
Неочевидные аспекты, о которых мало говорят
Толщина проволоки и чистота поверхности
Если вы работаете над ювелирными изделиями или высокоточными микроэлементами, иногда требуется ультратонкая проволока диаметром менее 0,1 мм. Такая «нить» способна прорезать материал с невероятной точностью, но скорость при этом будет весьма умеренной. Зато качество кромки — почти безупречное.
Инверсия подходов в технологическом процессе
Заметьте, что при электроразряде вы фактически меняете обычное представление об обработке: чаще «проблемное место» — это не прочность заготовки, а условия создания искрового канала. Если канал формируется корректно, твёрдость или толщину заготовки можно считать уже не таким страшным препятствием. В этом и заключается своего рода «переворот сознания» для тех, кто впервые знакомится с EDM.
Перефразируя специалистов:
«Если раньше нам нужно было преодолевать сопротивление металла твёрдым режущим инструментом, то теперь мы позволяем электрической дуге выполнять за нас эту тяжёлую работу, практически не прикасаясь к материалу». Именно так описывают происходящее мастера, которые давно освоили эту методику.
Вопрос к вам:
Планируете ли вы интегрировать электроэрозионный участок в свою линию или полагаетесь на аутсорсинг? Иногда проще заключить договор со специализированной компанией, имеющей парк EDM-станков и штат опытных операторов. Это даёт возможность получать высокоточные детали без капвложений в собственную технику и её обслуживание.
Организация рабочего места и экология
- Безопасность
Работа с электрическим разрядом и диэлектрической жидкостью требует хорошей вентиляции. Важно следить, чтобы пары не накапливались, а остатки масла не попадали в окружающую среду. - Охрана труда
Оператор должен иметь специальную одежду, а также регулярно проверять состояние станка. Наличие датчиков температуры и уровня жидкости позволит вовремя отреагировать на внештатные ситуации. - Очистка диэлектрика
Существуют системы фильтрации, позволяющие использовать жидкость повторно. Это снижает затраты и делает производство более экологичным.
Как правильно выбрать EDM-станок?
- Определитесь с задачами: нужны ли вам крупные детали или микропрецизионные компоненты? От этого зависит и габарит станка, и диапазон настроек.
- Проверьте надёжность поставщика: многие ориентируются на известные международные бренды, но иногда локальные производители предлагают более выгодные условия и полноценную гарантийную поддержку.
- Учитывайте перспективу роста: если ваш бизнес планирует расширяться, подумайте, не потребуется ли вам более продвинутый вариант оборудования, чтобы не заниматься перепродажей через год.
Пример из практики:
Когда одно машиностроительное предприятие решило модернизировать свой производственный парк, они сначала купили небольшой «учебный» EDM-станок, чтобы отработать технологию и обучить специалистов. Спустя полгода заказов на микрообработку стало так много, что они приобрели полноценную высокоскоростную установку с большим рабочим столом и автоматической подачей проволоки. Обученный персонал уже не боялся сложностей настройки, а клиенты были довольны скоростью и качеством. Такой подход продемонстрировал, что постепенный рост даёт возможность избежать резких финансовых вложений.
Таким образом, электроэрозионная обработка — это целая экосистема знаний, оборудования и практического опыта. От понимания фундаментальных принципов (искрового взаимодействия в диэлектрической среде) и грамотных настроек до оптимальной логистики расходных материалов и организации рабочего места — все элементы связаны между собой. При налаженном процессе вы получаете инструмент, открывающий практически неограниченные возможности для создания деталей любой сложности, будь то микроскопические компоненты для медицинских устройств или массивные пресс-формы.
Если вы — инженер или предприниматель, который старается вывести свою компанию на новый уровень, то обратите внимание на электроискровые методы. Это та самая инновация, которая может стать ключом к повышению конкурентоспособности и увеличению ассортимента.
- Coil Coating — Преимущества перед традиционной окраской
- Запчасти для спецтехники 2025: секреты выбора оригинальных деталей и экономия на обслуживании
- От катанки до небоскреба: Как рождается стальной крепеж, держащий мир на своих плечах
- Котельное оборудование: виды, характеристики и применение в промышленности
- Ремонт техники Apple в 2025: Все что нужно знать каждому владельцу
- Автопогрузчик: Ваш железный помощник в мире грузов – выбираем технику с умом
- Плазменная резка металла: ключевые области применения в промышленности и искусстве
- Поставки металлопроката: как выбрать надежного поставщика и оптимизировать затраты
- Сдать вторсырье в Екатеринбурге: как превратить мусор в ресурс и помочь планете
- Червячные хомуты: Секрет надежного соединения, о котором вы не задумывались